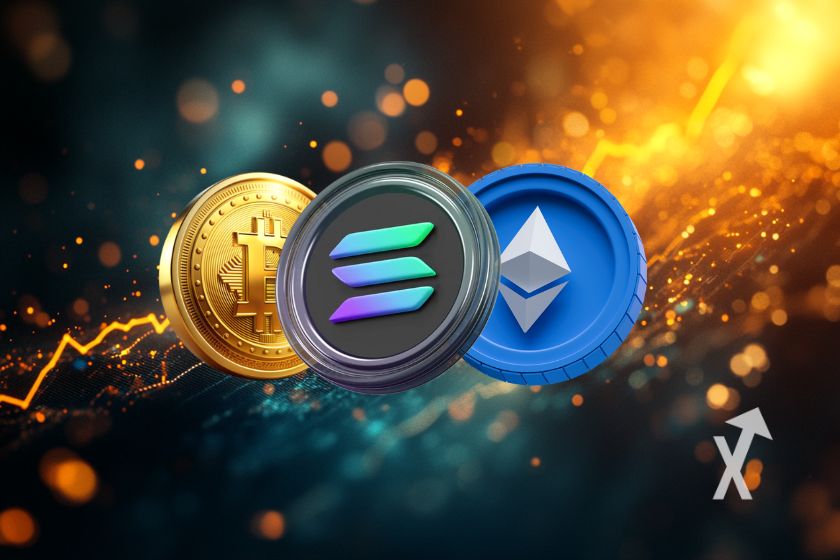
Cryptocurrency prices are volatile and unpredictable, but a deep analysis of market trends can provide valuable insights into future price movements. Find out what experts predict for top cryptos like BTC, ETH, and XRP.
Written by Charles Ledoux
Translated on June 26, 2025 at 11:04 by marie_redacteur
Despite geopolitical tensions, Bitcoin (BTC) has managed to make a significant comeback in recent days. After dropping below the $100,000 mark, BTC has regained ground, surpassing its moving averages, a sign of strong support at lower levels. Analysts believe that the price may now defend the area between the downtrend line and its all-time high at $111,980.
If buyers manage to keep BTC above the moving averages and its Ichimoku cloud on a daily basis, a new attempt to break the all-time high seems likely. However, the absence of a clear catalyst could prolong the consolidation of Bitcoin within the current range for some time.
On the altcoin side, the situation is more mixed. Ethereum (ETH) has indeed bounced back from the $2,111 level, reaching the 20-day moving average. However, a move beyond this resistance will be required to propel ETH towards $2,738 and $2,879.
XRP has also vigorously bounced back from the support at $2, hinting at a possible recovery towards $3 and $3.40. Nevertheless, the consolidation between $2 and $2.65 could still continue for a few more days.
Regarding Binance Coin (BNB), Solana (SOL), Dogecoin (DOGE), and Cardano (ADA), the outlook also remains mixed. These altcoins have indeed managed to recover from their recent lows but are still struggling to break key resistance levels. For example, Solana will need to break the resistance at $149 to turn bullish again.
In summary, the cryptocurrency market remains highly volatile and influenced by multiple factors, from geopolitical tensions to central bank decisions. Investors must remain extremely vigilant and carefully monitor the support and resistance levels of the top cryptos.
For now, altcoins are still awaiting validation of a major move by Bitcoin. Most of them are still in a short-term bearish structure. Nonetheless, their daily Woodies CCI is about to turn positive, indicating that a bullish reversal is near.
More on this topic :
Charles Ledoux is a Bitcoin and blockchain technology specialist. A graduate of the Crypto Academy, he has been a Bitcoin miner for over a year. He has written numerous masterclasses to educate newcomers to the industry and has authored over 2,000 articles on cryptocurrency. Now, he aims to share his passion for crypto through his articles for InvestX.
DISCLAIMER
This article is for informational purposes only and should not be considered as investment advice. Trading cryptocurrencies involves risks, and it is important not to invest more than you can afford to lose.
InvestX is not responsible for the quality of the products or services presented on this page and cannot be held liable, directly or indirectly, for any damage or loss caused by the use of any product or service featured in this article. Investments in crypto assets are inherently risky; readers should conduct their own research before taking any action and invest only within their financial means. This article does not constitute investment advice.
Risk Warning : Trading financial instruments and/or cryptocurrencies carries a high level of risk, including the possibility of losing all or part of your investment. It may not be suitable for all investors. Cryptocurrency prices are highly volatile and can be influenced by external factors such as financial, regulatory, or political events. Margin trading increases financial risks.
CFDs (Contracts for Difference) are complex instruments with a high risk of rapid capital loss due to leverage. Between 74% and 89% of retail investor accounts lose money when trading CFDs. You should assess whether you understand how CFDs work and whether you can afford to take the high risk of losing your money.
Before engaging in financial or cryptocurrency trading, you must be fully informed about the associated risks and fees, carefully evaluate your investment objectives, level of experience, and risk tolerance, and seek professional advice if needed. InvestX.fr and the InvestX application may provide general market commentary, which does not constitute investment advice and should not be interpreted as such. Please consult an independent financial advisor for any investment-related questions. InvestX.fr disclaims any liability for errors, misinvestments, inaccuracies, or omissions and does not guarantee the accuracy or completeness of the information, texts, graphics, links, or other materials provided.
Some of the partners featured on this site may not be regulated in your country. It is your responsibility to verify the compliance of these services with local regulations before using them.
© InvestX 2025
source